The power source is a vital part of every electronics project. From solar energy and EVs to portable game consoles and smart phones, batteries make up the vast majority of these power sources. So why do most engineers never learn about battery sizing in school? I’ll walk you through how to choose the right battery for your project and outline the practical details they don’t teach in school.
This post will cover the following topics:
- Define and detail important battery specifications (voltage / current, energy density, lifecycle, etc.)
- How to size a battery (with examples)
- Trade study of 14 most common battery chemistries
Primary vs. Secondary
The first thing to consider is if your application needs a primary or secondary battery. A primary battery is one that cannot be re-charged and a secondary battery is one that can. Primary batteries tend to have low self discharge rates around 2% a year. Primary batteries can provide longer shelf life and are much cheaper for low usage devices.
Battery Specifications
To choose the right battery for your project, you need to understand which specifications are important and what they mean. This will allow you to make the most informed decision for your given application. I have defined the essentials below.
Voltage / Current:
Voltage
If you need a refresher, this Fluke article outlines a basic overview of voltage. What you are powering (Your load) will determine the battery voltage you need. For example, most microcontrollers need 3.3V whereas brushless DC (BLDC) motors could need 100V or more. The closer you can get the battery voltage to the required load voltage, the longer runtime you’ll get. There are additional considerations involving battery voltage aside from just pack voltage.
Cell Voltage Ratings
Voltage in a battery is dependent on the cell chemistry. The battery voltage in equilibrium is called the nominal voltage. So nominal voltage is the cell voltage after a charge. For Lithium Ion cells, this is 4.2V. Permanent damage will occur if cells are discharged below a certain voltage. This is known as the cutoff voltage. Lithium Ion cells have a cutoff voltage of ~2.8V.
Smaller cell voltages means batteries have to be placed in series to achieve higher pack voltages. Placing cells in series adds the voltage of the cells together. Most applications need at least 5V and most chemistries produce 1.2 – 4.2V. Another major consideration when determining battery voltage is voltage sag effect.
Voltage Sag
As a cell discharges under load, the voltage will drop over time following a discharge curve. Different cell chemistries have different discharge curves. This voltage drop over time is referred to as voltage sag. This means as your application is running, the voltage of the battery could drop as much as 35% when under load. Similar effects take place when charging but in the opposite direction. The graphic below shows discharge curves for a few common cell chemistries. Note that these discharge curves represent each battery operating at their rated currents.
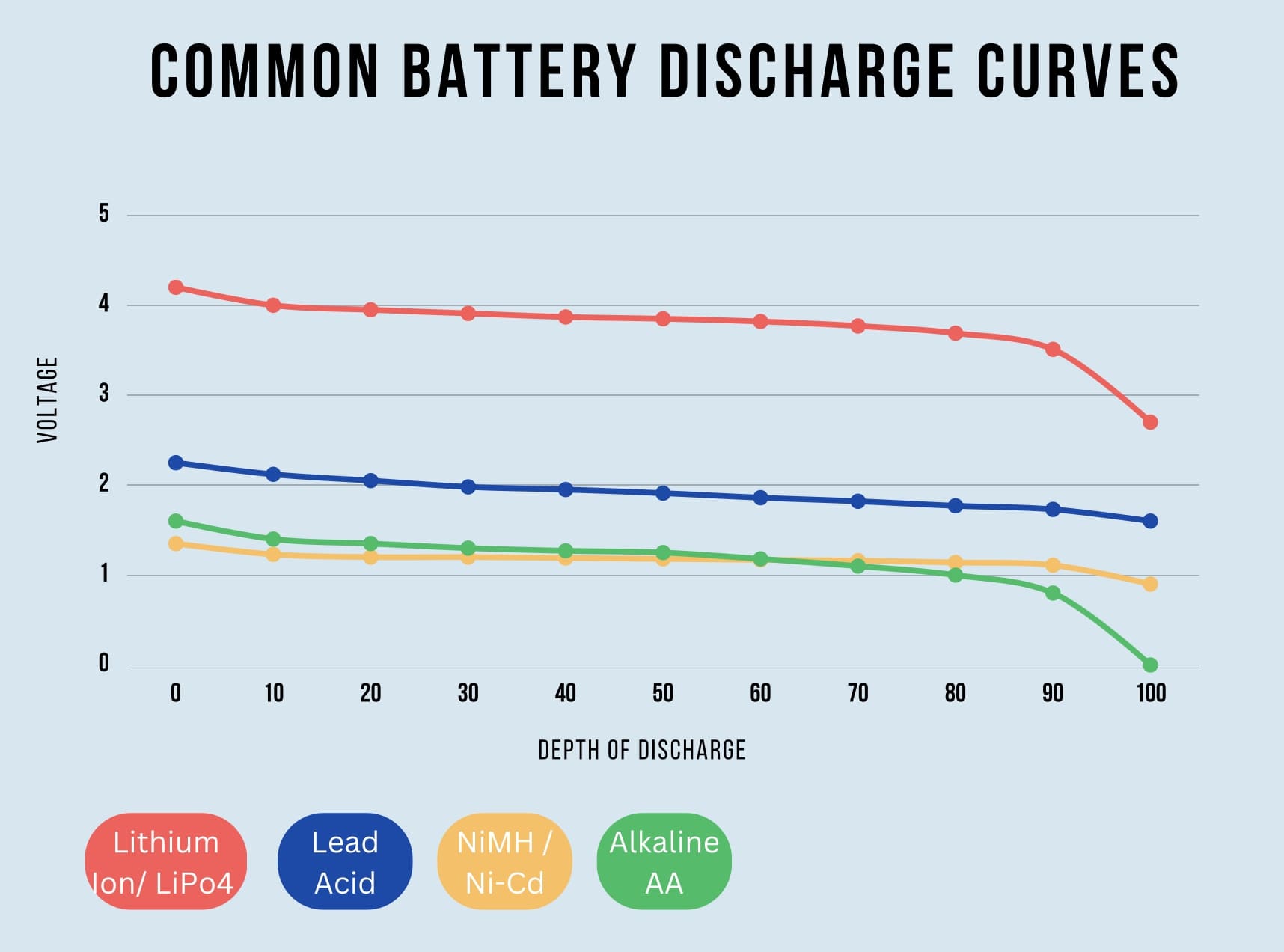
Current
The following Fluke article has a basic refresher of current if needed. Battery current is a main driver of how much runtime you will get out of a battery. Battery current is expressed in Amp-Hours (Ah). Amp hours is the amount of current sourced from the battery that would cause it to fully discharge in 1 hour. For example, if you have a 5Ah battery and a load that draws 2.5A, your battery will run for 2 hours. Along with Amp Hours, batteries also specify something called capacity which is closely related to the current rating.
Capacity
Capacity shares its units with current rating and is a short hand way to talk about battery current. If the nominal current rating is 5Ah like in our example above, the battery has a capacity of 5Ah. In other words 1C is equal to 5Ah. Batteries specify the max charge current / max discharge current in terms of capacity. Most lithium ion batteries have a max pulse discharge current of 2C and a max continuous charge current of .5C. But you can supply up to 150C in very short bursts. With capacity and current ratings defined, let’s understand the short comings.
Capacity and Actual Runtime
Note that in almost all cases, your actual battery run time will be less than ideal. In my previous example, I stated that a 5Ah battery with load drawing 2.5A will have a runtime of 2 hours. This equation is true on paper but in practice, the actual runtime will heavily depend on current draw. The higher the discharge rate gets above .5C (2.5A in our example), the harder the battery has to work to produce the current. This drops it’s efficiency.
This Pololu article on battery capacity has a great analogy on discharge current vs runtime. It states, “The current and capacity for a battery are like the speed (current) and range (capacity) of a car. If your car has a range of 300 miles, you can go 30 miles an hour for ten hours or 60 miles and hour for five hours. But your efficiency gets worse with speed so by the time you go 60 miles per hour you might run out of gas after only four hours for a range of 240 miles.”
Series vs parallel
A quick note on battery cells in series vs parallel. As stated above, placing battery cells in series adds their voltage together but placing cells in parallel adds their currents together. Battery packs are denoted using S (series) and P (parallel). For example, a 6S2P pack has two parallel blocks of 6 cells in series. For lithium ion cells with a capacity of 2.5A, a 6S2P pack would equate to ~24V (6*4.2V) and 5Ah(2*2.5Ah).
Key points:
- Nominal voltage: Max cell voltage
- Cutoff Voltage: Secondary batteries have hard discharge limit
- Voltage sag: Voltage will sag over time during operation
- Battery runtime (Hours) = Capacity (Ah) / load current draw (A)
- Runtime calculation becomes less ideal as current draw increases
- Cells in series add their voltage together
- Cells in parallel add their current together
Temperature
Temperature has to be considered when choosing the right battery for your project. Battery capacity decreases as temperature drops. Battery specifications for capacity are rated at room temperature (25 degrees C). Large temperature swings can also affect the performance and lifecycle of the battery. For lead acid batteries, each 8 degree C rise in temperature causes a halving of lifecycle. Lifecycle is the number of charge / discharges a battery can withstand over it’s entire life. Nearly all chemistries share these same relationships with temperature to some degree. In order to determine which chemistries have suitable temperature ratings for an application, battery discharge curves are once again used.
Discharge Curves and Temperature
The plot below shows battery voltage vs capacity at various temperatures for lithium ion cells. Note that as temperature drops, voltage sag happens much quicker limiting capacity and battery runtime. Also notice that capacity actually increases with temperature. When heated up, the chemical reactions inside battery cells quickens, increasing capacity and performance. But there is a negative effect to this as well. When running at high temperatures, battery lifecycle will decrease at a faster rate. Lithium ion cells can even catch fire if the temperature exceeds 80 degrees C.
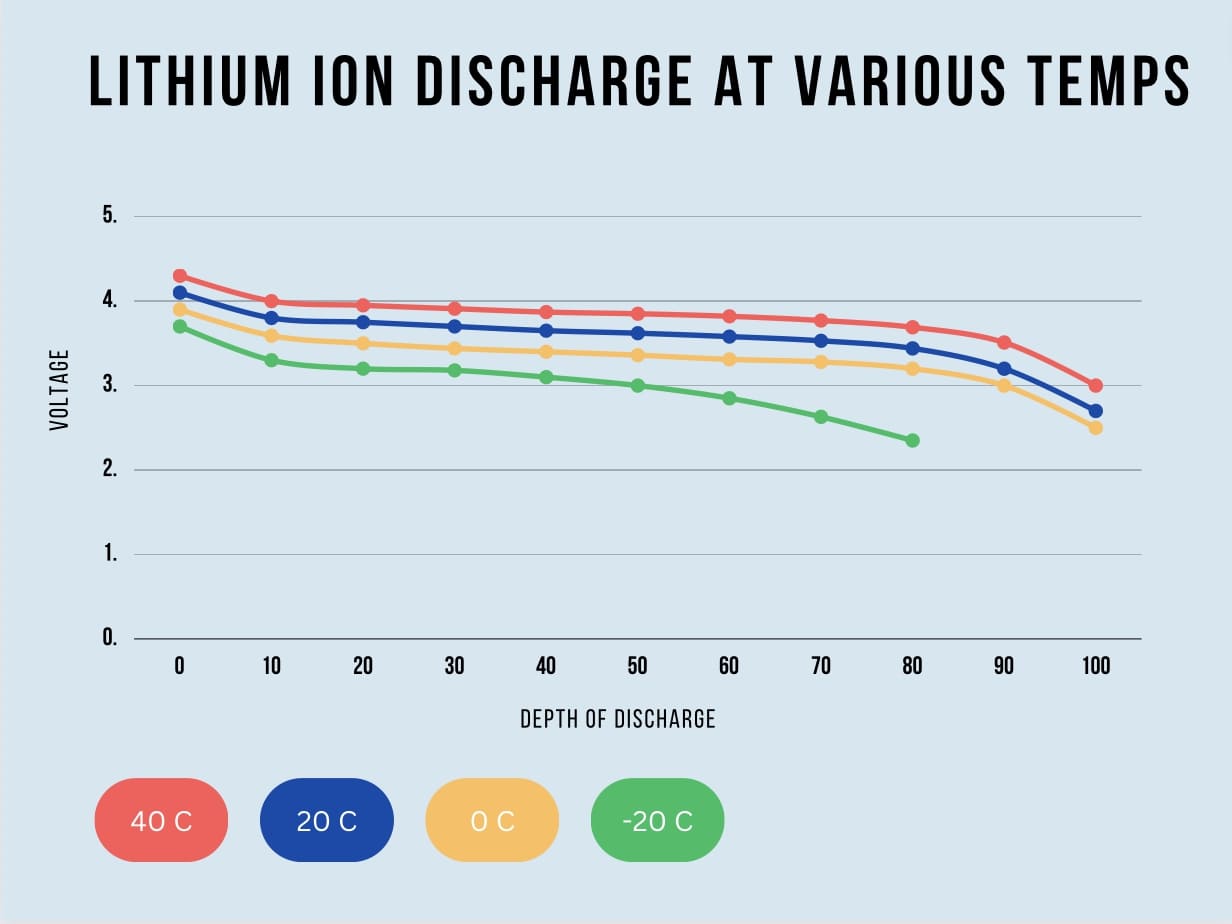
Key Points:
- Battery lifecycle will decrease at a faster rate if operated at high temperatures
- As temperature decreases voltage sag will occur at a faster rate limiting capacity and runtime
Energy Density
Energy density is how much energy a battery contains in proportion to its volume (Wh/L). Another way to think of energy density is as the amount of runtime in relation to the battery’s size. Higher energy density means a smaller battery that can store more energy which is always a good thing. Battery power is defined in Wh (Watt Hours). Watt Hours are defined as Voltage * Amp Hours. Watt Hours specify how much power in watts the battery can produce for one hour.
Another closely related term is specific energy. Specific energy relates energy to battery weight (Wh/Kg) instead of volume (Wh/L). Although energy density tells you how much energy a battery can store, it does not tell you how quickly it can release this energy.
Power Density
Power density is how fast a device can discharge its stored energy. A battery with high power density and low energy density can discharge at very high rates but will drain the battery quickly. Power density is defined as W/kg (Watts / Kilogram) as apposed to energy density which is Wh/Kg (Watt Hours / Kilogram). This subtle difference has a big impact. As you can see, energy density has a time element incorporated which measures how long the battery can supply a given amount of power. Power density on the other hand is a measure of power at a given time or a measure of instantaneous power. Power density is proportional to current so power density increases as the max battery current increases.
Key Points:
- Energy density: Energy battery can store / batter volume
- Higher means battery will last longer and be smaller
- Specific Energy: Energy battery can store / battery weight
- Higher means battery will last longer and be lighter weight
- Power Density: How quickly battery can output stored energy
- Higher means can push more current
Discharge / Self Discharge Rate
As defined in the Voltage section, discharge curves show how the battery voltage sags over time and depends on temperature and current draw. Self discharge is the phenomenon where a battery drains while it is not in use. All batteries will self discharge but the rate of self discharge will depend on cell chemistry.
Most primary batteries have a low self discharge rate. They are one time use devices and need to have a very long shelf life. Self discharge rates are affected by temperature, state of charge and other parameters. Below is a graphic showing a comparison of various cell chemistries self discharge rates.
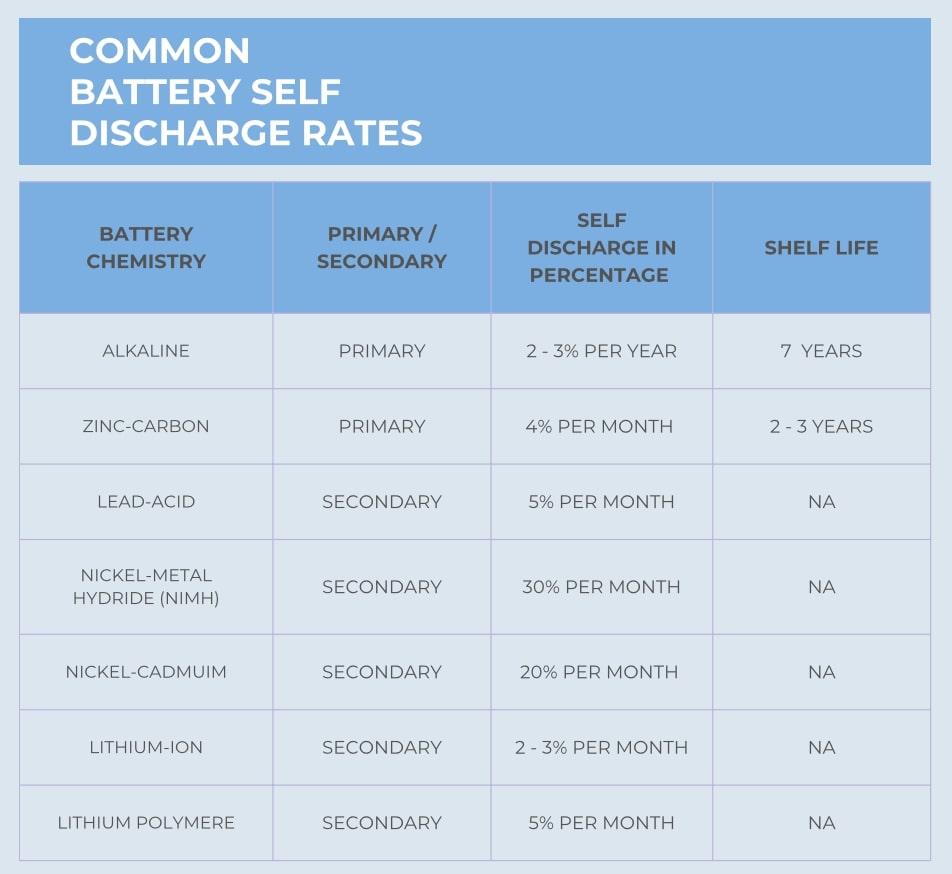
Key Points:
- All batteries will have some amount of self discharge when not being used
- Primary batteries will generally have smaller self discharge rates
Depth of Discharge (DoD) / State of Charge (SoC)
Depth of discharge is defined as how much the battery has drained as a percentage of its overall capacity. That is:
This can be expressed as a percentage or in Ah. State of charge is the opposite and represents how fully charged the battery is in terms of percentage or Ah. These measurements are important because most battery lifecycles will be dramatically reduced if discharged below their DoD rating. Some modern batteries have much larger DoD ratings called deep cycle batteries.
Deep Cycle Batteries
Deep cycle batteries can generally handle a DoD of 80% or more depending on the battery chemistry. They are a good choice for applications in need of longer battery life with constant current draw. Applications in need of short bursts of energy might not benefit much from a deep cycle battery.
Although deep cycle batteries can handle greater DoD, limiting DoD is still a good idea to extend battery lifecycle. So how do we know when we have reached our DoD and need to switch off the battery? We are all so used to having battery percentages reported on our phones and devices it seems like determining DoD and SoC would be trivial but it can be harder than expected.
Coulomb Counting
SoC and DoD can be difficult to measure since battery voltage can vary with temperature, discharge rates, age and more. Because of this, the battery voltage cannot be used to deduce the DoD / SoC. Something called Coulomb counting is often used instead. Coulomb Counting uses the measurement of current flow to and from the battery to estimate SoC / DoD.
Coulomb Counting is still not perfect as there are energy losses in the battery. These energy loses manifest as heat and the battery output current will never exactly match the input current. But it provides a close enough estimation for a complex problem. When looking for battery management or monitoring systems (BMS), ensure it is using coulomb counting and not just voltage monitoring. Any BMS worth buying should have built in under voltage protection that will enforce DoD limits.
Key Points:
- Depth of Discharge (DoD): How much battery has drained as percentage of its overall capacity
- State of Charge (SoC): How fully a battery is charged in terms of percentage
- Deep cycle batteries can handle a higher DoD (usually 80% of more)
- Deep cycle batteries are best for constant current applications that need long battery life
- Simple voltage monitoring to determine DoD or SoC is not sufficient
- Coulomb Counting is accepted as industry standard so ensure your monitoring systems does not use voltage monitoring.
Number of charge cycles (Lifecycle)
Lifecycle is the number of charge / discharge cycles a battery can withstand over its life. Obviously this only applies to secondary batteries which can be recharged. Over time, the battery loses the ability to charge back to its original capacity. Most manufactures use the metric 80% of the original capacity to define when the battery has reached its full “lifecycle”. Meaning lifecycle is the number of times you can recharge a battery until it can only reach 80% of its original capacity. The battery can be used after this point but will continue to degrade. Different cell chemistries have different lifecycles.
Getting the Most Life Out of Your Battery
How can you optimize your battery lifecycle? Some tips to ensure the best lifecycle are to operate at mild temperatures, limit your depth of discharge and complete full charge cycles at slow rates. For lead acid batteries, do not discharge the battery more than 50% depth of discharge. For lithium ion batteries you can likely get away with 80% discharges. Below is a graphic containing various cell chemistries and their lifecycles / recommended depth of discharge.
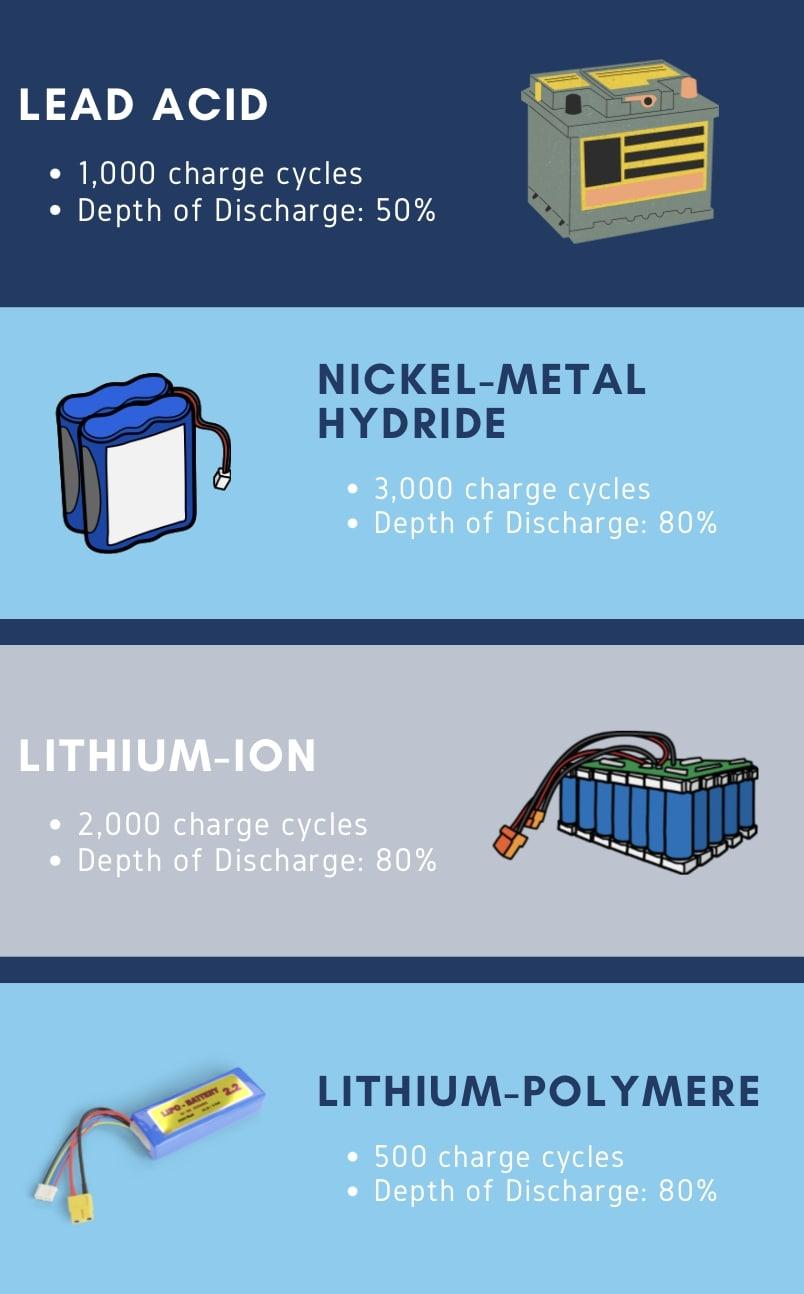
Key Points:
- Battery lifecycle: The number of times a battery can be recharged until it can only reach 80% of it’s original capacity or lower.
- Different chemistries have different lifecycles from hundreds to thousands of charge / discharge cycles
- Optimize lifecycle by avoiding extreme temperatures, limiting depth of discharge and always completing full charges slowly
Battery Management System (BMS)
Battery management systems (BMS) are a huge consideration when choosing a battery for your project. This can add complexity and cost but is very important. Some cell chemistries need a BMS and others do not. Lead Acid and Nickel Cadmium cells do not require a BMS but Lithium Ion cells do. This is due to the safety hazards Lithium Ion cells can cause with overheating.
When picking a BMS for a Lithium Ion packs there are some key features you need to check for. The most critical features that every BMS must have are under / over voltage protection and over temperature protection. If any cell deviates from the operating voltage ratings, the pack should be shutoff to save the battery lifecycle. Temperature protection is critical due to Lithium Ion’s tendency of thermal runways. This happens when the battery is not properly charged / discharged. In addition to these core features, the BMS should also implement what is called cell balancing.
Cell Balancing
Cell balancing in a BMS compensates for individual cells charging / discharging at different rates. If one or more cells in the pack are not closely matched in voltage when charged or discharged, it can cause all sorts of issues. Every cell is not identical and each one will have slightly different capacity and internal resistance. Or if there is damage to any one cell, that cell can reach the max charge voltage faster than the others. During charge, the damaged cell would cause a premature over-voltage condition. All other cells would not have reached their max charge and runtime would suffer. During discharge, a damaged cell could have less capacity than the others and cause a premature under-voltage condition. This would also result in a loss of usable battery capacity / runtime. In order to fight this, a BMS uses cell balancing to ensure all the cells are charged and discharged evenly. Most battery management systems have what is called passive balancing but more advanced systems have something called active balancing.
Passive vs Active Cell Balancing
Passive cell balancing refers to a system that only balances cells during charging. It does this by passively bleeding out charge on any cells that are experiencing over voltage. Active balancing distributes charge during both charging and discharging. Active cell balancing is less common and more expensive due to the added complexities.
Any off the shelf Lithium Ion battery pack worth buying should have a built in BMS. If building your own pack, there are some options that won’t break the bank. The most affordable option is a UK based brand, DALY. They sell a variety of sizes from 15A – 120A discharge ratings. Here is a link to where you can buy one. When purchasing a BMS, make sure it has the minimum features outlined below.
Key Points:
- Check if your chosen battery chemistry requires a BMS
- Ensure any BMS you purchase has the following minimum feature set
- Under / over voltage protection
- Over temperature protection
- Passive cell balancing
Charging
Charging requirements also need to be considered when choosing any secondary battery. Different cell chemistries require different charging procedures and thus different chargers. For example, lithium ion cells charge in three distinct phases. Phase one preconditioning ensures the cells are ready to receive full charge current. Phase two starts a constant current charge that boost the cells up to their rated 4.2V. And finally constant voltage charge tops off the batteries while maintaining a safe 4.2V per cell. Some lithium ion chargers also enable fast charging that give a cell its first 25 – 50% charge much faster.
On the other hand, NIMH batteries are very difficult to detect an accurate end of charge. For this reason, NIMH batteries are charged at much slower rates for longer amounts of time. This ensures the correct charge gets applied.
Total charge time required for your battery should be considered and will depend on size, chemistry, and charging methods.
Key Points:
- Ensure to buy a charger that matches your cell chemistry
- Charging time will vary between cell chemistries
Size / Shape / Weight
Size, shape and weight could be a critical part of choosing a battery for a project. Some cell chemistries have more options than others. Lithium ion cells come in a few different sizes but you are generally constrained to some variation of a standard cylindrical cell. Because of this, there is only so much you can do to customize the pack shape. Lead acid batteries need a liquid electrolyte so are generally constrained to some variation of a motorcycle or car battery package type. But there are a couple cell chemistries with more flexibility in packaging.
Custom Pack Sizes
Lithium Polymer (LiPo) batteries are some of the most flexible when it comes to pack size and weight. LiPo batteries come in all shapes and sizes. These are pouch like batteries that use a gel base, making them very customizable. Generally, they come in rectangular or square packaging but I have seen cylindrical and even circular packaging as well. Nickel Metal Hydride (NIMH) batteries also have some room for flexibility. Although they mostly come in cylindrical packaging, the length and diameter of these cells can very greatly.
The less voltage / capacity needed, the more flexibility you have. Options become more limited as voltage / current requirements increase. In some projects, size and shape are not as important as weight. If battery weight is the only important parameter then try to pick the chemistry with the highest specific energy. This will give you the largest range vs battery weight.
Cost
While cost may seem like the most straight forward parameter when picking the right battery for your project, it is intertwined with a lot of other factors. The cost of your battery is directly proportional to how many cells you need. This depends on the voltage, capacity and energy density of the cells. A more expensive cell might have a higher capacity meaning you need less of them.
When determining costs, first you need to size your battery to get an idea of what voltage / capacity you need. Then you can work out how many cells of each battery type you would need before calculating costs. This is assuming you are building a pack from scratch and not just purchasing off the shelf.
Off the Shelf
If purchasing an off the shelf battery pack, you still need to start by sizing your battery. Once you know the needed voltage / capacity, find a few different options with varying chemistries. Read through the “Choosing the Right Battery Chemistry” section of this post and pick the pack that best meets your needs! When buying a pack off the shelf, ensure it has the necessary BMS and comes from a reputable source.
Safety / Durability
Battery safety is a critical part of any project design. In some cases like electric vehicles it can mean life or death. As always, battery safety depends on cell chemistry. Some chemistries are much safer and more stable than others. And in general most primary batteries have less risk of overheating than secondary batteries. The main safety concerns to consider are overheating, choking hazards and toxic outgassing during charging.
Each cell chemistry needs careful consideration of the risks, proper operating environments and a plan to minimize safety concerns. Lithium ion batteries have been known to overheat and even start fires. Store any unused or charging lithium ion batteries in a fireproof container. Charging certain battery chemistries like lead acid can produce toxic gas and should always be done in a well ventilated area. Never overcharge a battery and always ensure the proper BMS is being used and working.
Transportation
When thinking about how to choose the right battery for your project, transportation is often overlooked. Certain cell chemistries have restrictions on how they can be transported and shipped. Other chemistries even have shipping bans so it is important to research how this could effect your project cost and schedule. These bans mostly apply to newer chemistries but it’s always a good idea to check.
How to Size a Battery
Now that we have an understanding of the important battery specifications, we can properly size everything. Sizing is the most important step when choosing the right battery for your project. The first step is determining how much current your project will consume.
Calculating Current Draw
To determine the current of your load you can use average or max current. Sizing the battery based on the max current will be the most conservative estimate as it assumes your application is running at full power all the time. Using average current will be the most representative of normal use but might reduce runtime for extreme scenarios.
For my e-kayak project, the motor I selected specified a max continuous current draw of 12A at 24V. I decided to size my battery based on this max current rating so that I know I can run full power for my desired runtime. Once you know the max or average current draw of your load, you can calculate the battery size.
Using my e-kayak project as the example, my max continuous current draw is 12A at 24V. Since I wanted a best case runtime of about 2 hours, I needed to pick a battery with a capacity around 12A * 2 hours = 24Ah at 24V.
Note that this is an ideal calculation and runtime will end up being smaller. As I discussed in the “Current / Capacity” section, running a battery near its nominal capacity will drain it quicker so I will most likely end up with a range closer to 1.5 hours. For my e-kayak I was able to use the raw 24V battery output but this won’t work for some projects. Some projects call for obscure voltages or cannot handle any voltage discharge sag. In these cases, a voltage converter is needed which will effect the battery sizing calculations.
Battery Sizing with a Voltage Converter
Voltage converters scale an input voltage up or down to meet a required output. Buck and boost are the two most common type of DC to DC voltage converters. When using voltage converters, Watt Hours are used to calculate the battery size instead of Amp Hours. To calculate Watt Hours, you still need to determine the required current and voltage of your load in the same way as before. But now you will calculate the required power of your load using:
Let’s look at an example of how to calculate battery runtime with a voltage converter.
Sizing Example with Converter
Using the e-kayak example, my motor required 12A at 24V meaning a power draw of:
Now let’s say I want to determine the runtime of a 12V, 20Ah battery with a voltage converter to step 12V up to 24V. First I need to determine the Watt Hours of the battery using:
So ideally our battery can supply 240W for one hour and our load requires 288W to operate at max speed. To calculate our ideal runtime we divide the battery Wh by our load power draw:
But as always, the ideal case does not match reality. When the voltage converter scales 12V up to 24V, it will induce some efficiency loss that manifests as heat. This will lower our ideal runtime. A conservative estimate of this loss is 20% so taking our original estimate of .8333 hours and adding the efficiency loss, we get:
So our actual runtime with the voltage converter in the loop is .666 Hours. Below is a graphic outlining the battery sizing process from beginning to end!
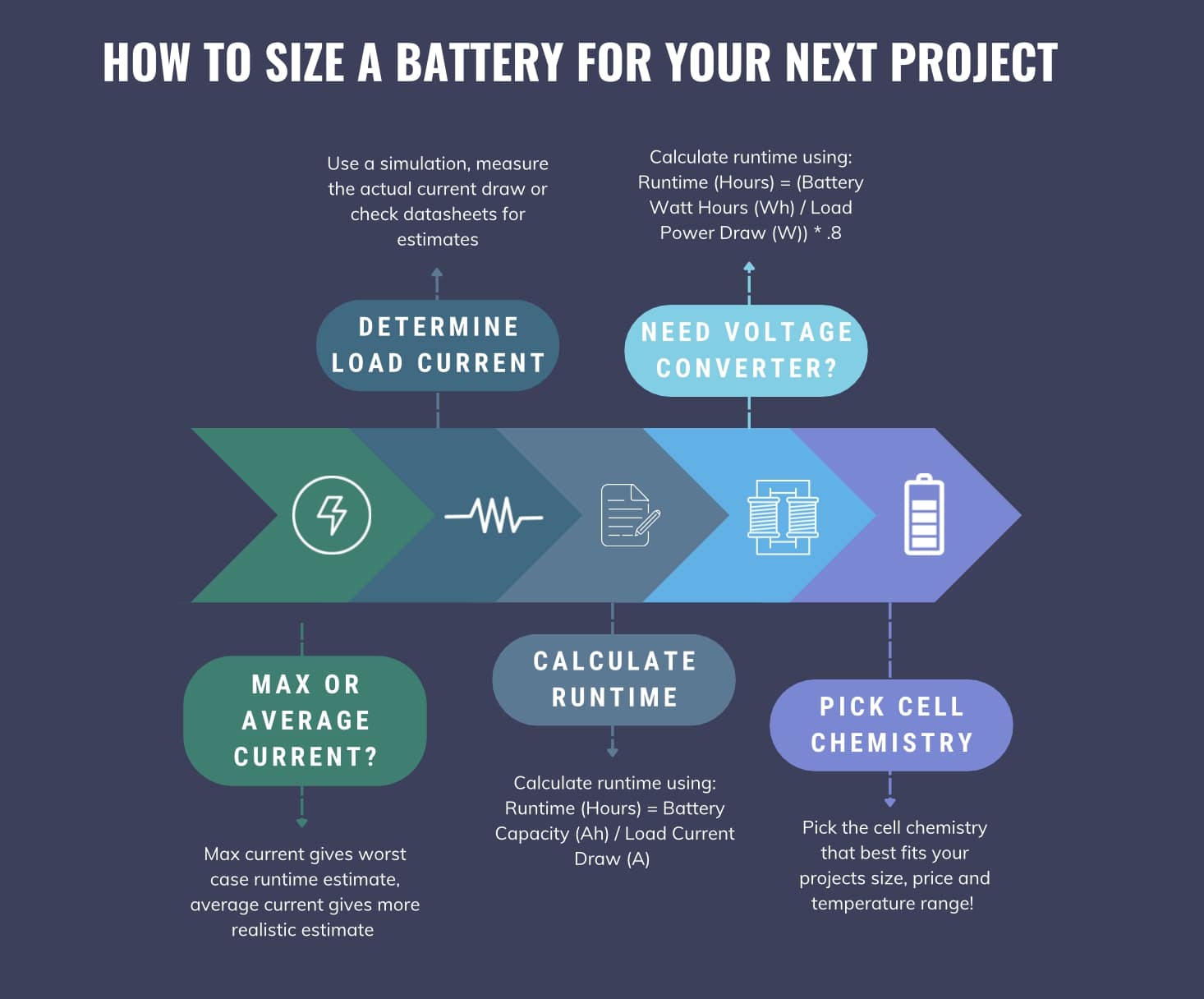
Key Points:
- Runtime (Hours) = Battery Capacity (Ah) / Load Current Draw (A)
- Assumes battery voltage matches required load voltage
- Can use average or max load current draw for estimation
- Runtime calculation becomes less ideal as current draw increases
- When using voltage converter:
- Runtime (Hours) = (Battery Watt Hours (Wh) / Load Power Draw (W)) * .8
Choosing the Right Battery Chemistry
With the battery sized, you now know what you’re looking for and can start comparing cell chemistries for things like price, temp range and size. There are tons of variations of battery chemistries, all with pros and cons. I have compiled all the key metrics of common cell chemistries in an easy to use graphic!
Primary
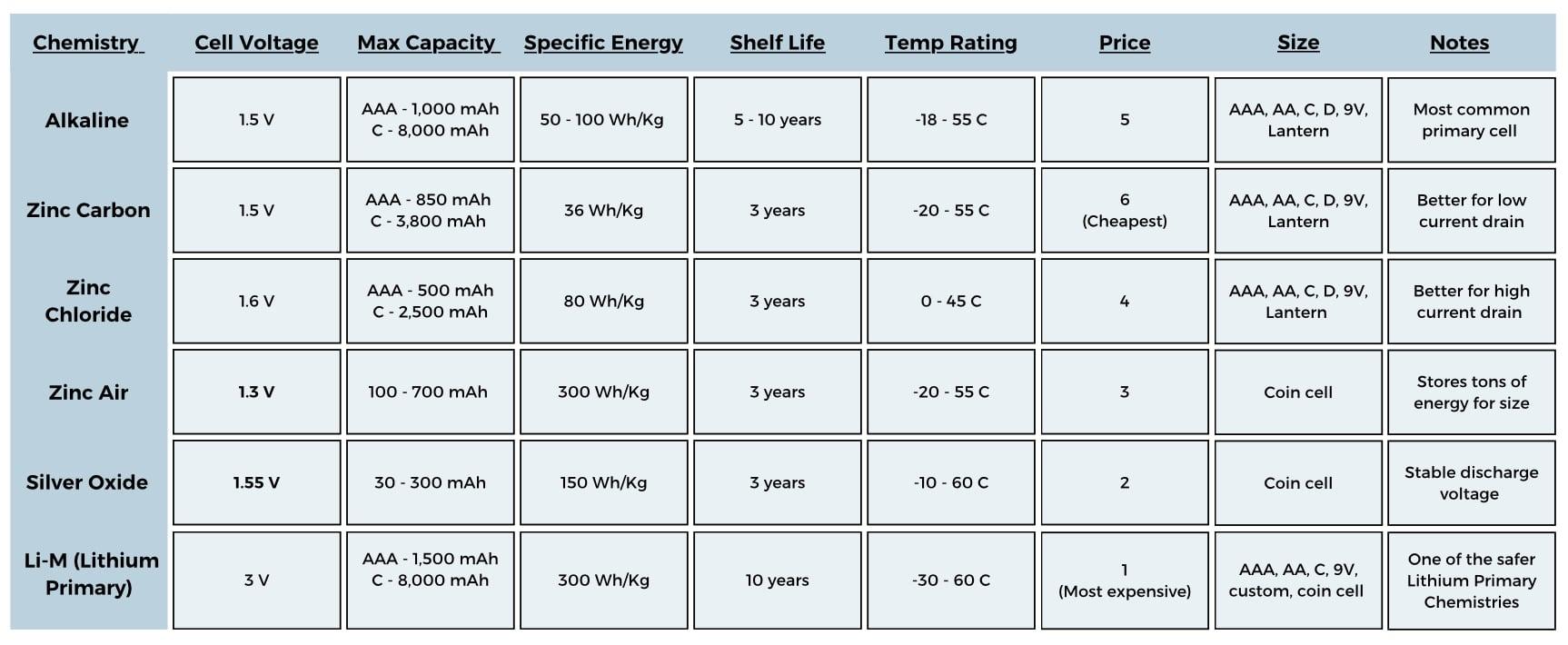
Secondary
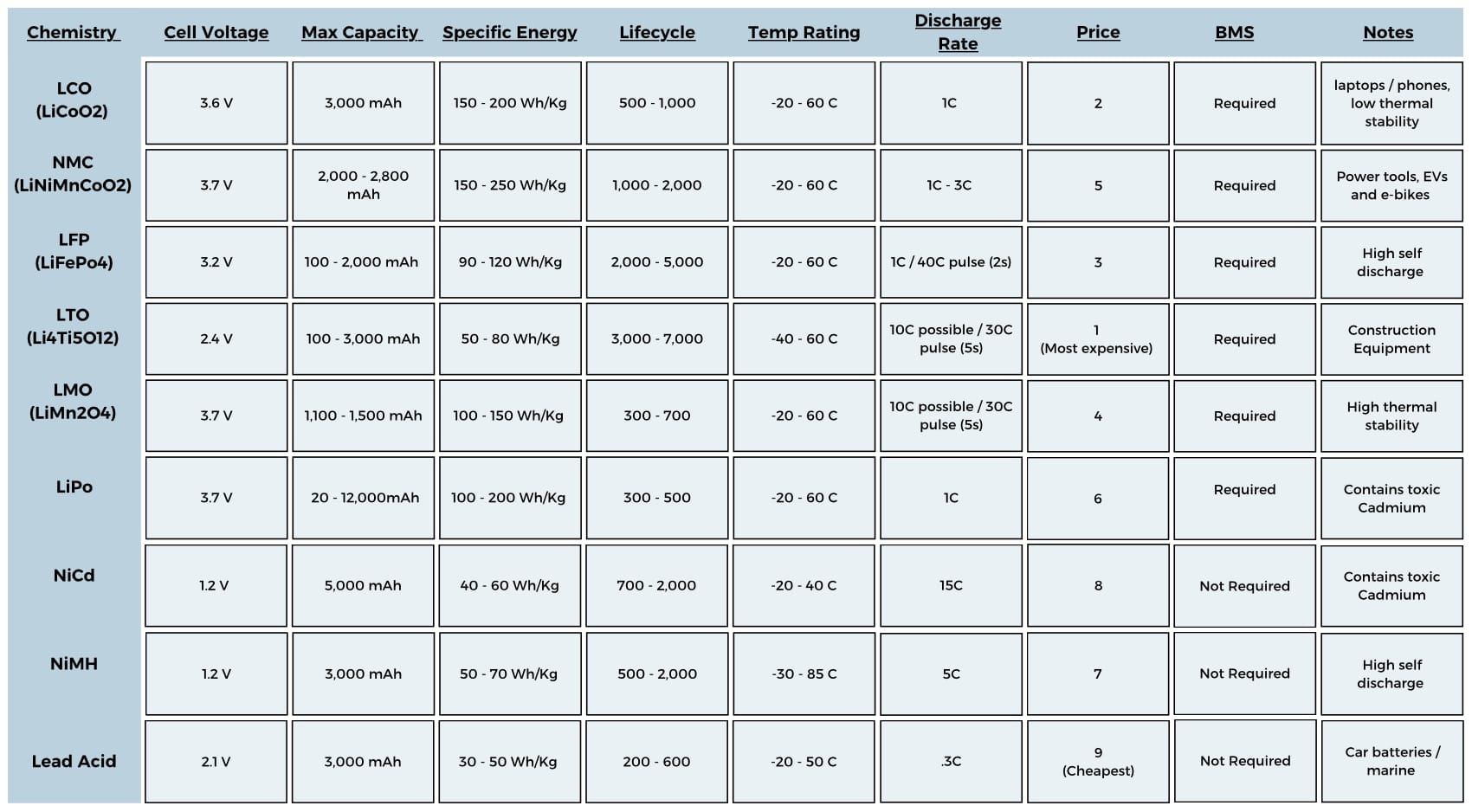
If you found this content interesting or useful, buy me a coffee!
Donations:
Bitcoin Wallet:
bc1q0vkx34w5y4yt5nq38a4rvk7gvgnxm2xv5lvyft